AKD Emulsion EXPEL Series
Negotiable Min Order Quantity Unit
- Required Quantity
-
- Place of Origin
- Payment Terms
- Negotiable
- Production method
- Negotiable
- Shipping / Lead Time
- Negotiable / Negotiable
- Keyword
- Category
- Catalyst & Chemical Auxiliaries
Taegwang Chemicals Co., Ltd.
- Country / Year Established
-
South Korea /
- Business type
- Others
- Verified Certificate
-
12
Product name | AKD Emulsion EXPEL Series | Certification | - |
---|---|---|---|
Category | Catalyst & Chemical Auxiliaries | Ingredients | - |
Keyword | - | Unit Size | - |
Brand name | - | Unit Weigh | - |
origin | Stock | - | |
Supply type | - | HS code | - |
Product Information
AKD Emulsion EXPEL Series
The driving forces for papermakers to change from acid to neutral papermaking are not always easy to establish, but probably the most important one is that neutral pHs allow the use of calcium carbonate, a relatively inexpensive and good quality filler. However, calcium carbonates cannot, for obvious reasons, be used in the acidic rosin-alum environment. Other important advantages of neutral papermaking which are often quoted are improved permanence, reduced machine corrosion and increased paper strength resulting from the increased fiber bonding obtained at higher pH.
A large number of cellulose reactive sizes have been considered over the years as neutral sizing agent, but they have found no commercial use. The most successful of neutral and alkaline sizes are the alkyl ketene dimmers (AKD) and the alkenyl succinic anhydrides (ASA). These are at opposite ends of the spectrum of reactivity and hydrolytic stability. AKDs are rather unreactive towards cellulose but have good hydrolytic stability. The reverse is true for ASAs.
EXPEL series, the neutral and alkaline sizing agents of TGchem, are emulsion products of AKD.
AKDs, which have known to be cellulose-reactive sizes, can react with the cellulose during the drying of the paper with the formation of beta-ketoesters. The ring-opening reaction always takes place at the acyl oxygen. AKD can also be hydrolyzed, giving an unstable beta-ketoacid, which decarboxylates to the corresponding ketone (Fig. 1).
In order to obtain good size degree with AKD, the following is required: Internal sizes are introduced at the wet end of the papermaking system, usually as colloidal suspensions, which are retained in the fiber network during sheet formation. During drying, and to some extent afterwards, they are able to spread and migrate, and undergo some form of interaction with the surface which allows orientation of the hydrophobic group and finally creation of a low-energy surface (Fig. 2).
As for AKD sizing, consequently, the sizing takes place in three consecutive steps; deposition-spreading-orientation or interaction. The orientation of AKD molecules is a rate-determining step in the development of size degree. Thus, one of the disadvantages in AKD sizing, delayed size development is due to the orientation of AKD.
AKD dispersions have considerable shelf life and hydrolysis can usually be avoided during storage. Low level of retention and high stock temperature are the main causes of hydrolysis of AKD in commercial use.
AKD is used primarily when the requirements are for hard sizing, e.g., liquid board. AKD gives a good resistance to fruit juice, lactic acid, etc. Another important area of use is CaCO3 containing fine papers. The addition level is usually between 0.06 and 0.2% calculated on dry pulp.
So-called sizing accelerators play a very important role in sizing with AKD. The reaction with cellulose can be catalyzed with additives so that the rate of reaction can be increased by a factor of at least 20. The important catalysts are HCO3- and basic polymers with amine groups.
The HCO3- ion has a unique ability to catalyze the reaction between AKD and cellulose. HCO3- ions can exist in a natural state in the system, e.g., when CaCO3 is used as filler, but it is also general practice to add Na2CO3 or NaHCO3 to the stock to increase the alkalinity.
Polymeric amines having amino groups with a free electron pair are classic sizing accelerators for AKD. Several different types of condensation polymers occur in commercial contexts. The polymeric sizing accelerator is added either to the AKD dispersion (rapid curing dispersion) or used separately as combined accelerator and retention aid. The effects of HCO3- and polymeric accelerators are synergistic.
EXPEL series can be divided into three categories: EXPEL-D series is classical AKD emulsion, which is very effective size used with fixing agent and retention aids, having an excellent thermal stability. Second is polymer-modified AKD emulsion, EXPEL-F series. EXPEL-F series can develop a sufficient size degree alone because the sizing accelerators are involved in the AKD emulsion. other one is modified by special agent, EXPEL-X series. EXPEL-X series can extremely high size degree, fast-cure, self-cure. Above all, EXPEL-X series can develops size degree at size press.
1. Typical Properties
EXPEL-125X
|
EXPEL-150D
|
EXPEL-150F
|
EXPEL-200D
|
|
Appearance
|
milky white liquid
|
|||
Active content(%)
|
12.0~13.0
|
15.0~16.0
|
15.0~16.0
|
19.5~20.5
|
Bulk viscosity(cps, 25°C)
|
<20
|
<15
|
<20
|
5~10
|
Specific gravity(Ave.)
|
1.00~1.01
|
1.00~1.01
|
1.00~1.01
|
1.00~1.01
|
pH
|
2.5~3.5
|
2.5~3.5
|
2.5~3.5
|
2.8~3.8
|
Storage temp.(°C)
|
5~30
|
5~30
|
5~30
|
5~30
|
Shelf life(Months)
|
1
|
3
|
3
|
3
|
2. Packaging
Plastic pails
|
Metalic drums
|
Schutz container
|
Other sizes
|
20kg
|
200kg
|
1,000kg
|
-
|
3. Heath and Safety
We know of no ill effects that could have resulted from using EXPEL-200D for the purpose for which it is intended and from processing it in accordance with current practice. EXPEL-200D does not exert any harmful effects on health, provided it is used properly.
These data are given for information only. They do not constitute a specification and no liability is assumed, nor freedom from any existing patents.
We do not guarantee the applicability or the accuracy of this information and the suitability of our products in any given situation, since we cannot anticipate the many different conditions under which our products may be used.
B2B Trade
Price (FOB) | Negotiable | transportation | - |
---|---|---|---|
MOQ | Negotiable | Leadtime | Negotiable |
Payment Options | Negotiable | Shipping time | Negotiable |
- President
- Mintae Park
- Address
- 229, Mugeuk-ro, Geumwang-eup, Eumseong-gun, Chungcheongbuk-do, Korea
- Product Category
- Catalyst & Chemical Auxiliaries
- No. of Total Employees
- 1-50
- Company introduction
-
Taegwang Chemicals Co., Ltd. is a leader in the development and production of paper additives in Korea. Started out as Taegwang Chemicals Company in 1982 which was our first step into paper chemicals industry, we have been growing and expanding ever since. In 1987, we re-established as Taegwang Chemicals Co., Ltd. with our accumulated technological know-how and expertise to fulfill our customers' needs and meet their requirements.
Our success has been resulted from continuous and thriving effort in development and improvement of our products while accumulating new and advanced technologies. It is no wonder that we, Taegwang, are the first in Korea to develop and supply alkaline sizing agents (AKD emulsion size) which contributes cost reduction and environmental impacts as well as improvements of quality for paper industry in Korea.
Since 1987, Taegwang has been providing technical aids to paper industries, which converted for alkaline papermaking, and Taegwang is now recognized as the leader in technology for alkaline papermaking in Korea. Our major product lines are AKD SIZING AGENTS, ROSIN-BASED SIZING AGENTS, FIXING AGENTS, WET- & DRY-STRENGTH AGENTS, DYE FIXING AGENTS, RETENTION AIDS (PROGRAMS), and ANIONIC TRASH CATCHERS.
We will not stop here, but continually thrive and step forward until we become a leader in the world-wide paper chemicals industry.
- Main Product
Related Products
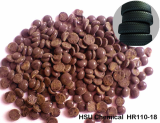
C9 Petroleum Resin for Tire Rubber Compound softening oil
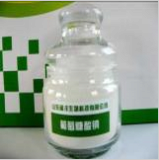
glucolactone/Glucono-δ-lactone(GDL)
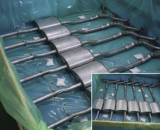
VCI Desiccant GVD100
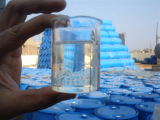
CHLORINATED PARAFFIN
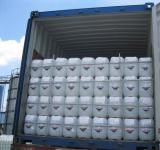
Phosphoric Acid 75%/81%/85% Food Grade