PU DIPPING MACHINES, KNITTED GLOVE COATING MACHINES, HAND PROTECTION GLOVES COATING MACHINES
TOP QUALITY GLOVES DIPPING MACHINE; HORIZONTAL RUNNING TYPE PU COATING MACHINE
Negotiable Min Order Quantity Unit
- Required Quantity
-
- Place of Origin
- South Korea
- Brand name
- Plama (I'm here for you)
- Payment Terms
- L/C
- Production method
- Available
- Shipping / Lead Time
- Negotiable / Negotiable
PLAMA WORLDWIDE TECH CO., LTD
- Verified Certificate
-
16
Product name | PU DIPPING MACHINES, KNITTED GLOVE COATING MACHINES, HAND PROTECTION GLOVES COATING MACHINES | Certification | - |
---|---|---|---|
Category |
Other Chemical Machinery Equipment
Coating Suppliles Safety Gloves |
Material | COAGULANT TRAY,DIPPING TRAY,GLOVES AUTOMATIC TAKEOUT UNIT,GLOVES DRYING CHAMBERS,LEACHING WATER TANKS |
Keyword | gloves pu dipping mc , gloves pu coating mc. , hand protection gloves coating mc. , cut resistance gloves pu coating mc | Unit Size | - |
Brand name | Plama (I'm here for you) | Unit Weigh | - |
origin | South Korea | Stock | 0 |
Supply type | Available | HS code | 010119 |
Product Information
▣ A DETAILED REPORT RELATED TO THE PU DIPPING MACHINE.
♣ Offer sheet we send consists of the following contents and conditions.
1. Dipping machine is a horizontal running type and is designed to produce palm coated gloves or halfcoated gloves.
2. Dipping machine can coat PU on liners knitted with Nylon / Polyester / TC / Kevlar yarns. However, PU coating quality is determined by the knitting method of the liner, the gauge of the knitting machine, and the covering method of the yarn.
3. The dimension of the dipping machine is based on the standard specifications that we supply all over the world.
4. The production of coating gloves is based on 900~1300 pairs per hour. This criterion is the production volume when the dipping machine is operated by a trained operator.
5. And in order to produce high-quality PU coated gloves, the temperature and humidity inside the machine must be optimally maintained to suit the local environment. In the case of PU resin and DMF, moisture is easily absorbed. Excessive humidity and high temperature lead to poor PU coating.
(1) Ideal temperature of PU dipping section; 25~28℃
(2) Ideal humidity of PU dipping section; 21~27%
* The above temperature and humidity management is mainly applied to the PU dipping section, the PU resin spill section, and the DMF coagulator section of the dipping machine.
* In addition, the temperature and humidity recommended above may vary depending on the conditions of the factory and the local environmental conditions.
6. We supply 3 sets of main mixers (900 ltrs each) and 3 sets of feeding tanks (400 ltrs each) for mixing PU resin.
-Main mixers are installation in the Lap.
-Sub-mixers (resin feeders) are installation near at the PU dipping section. And these sub-mixers may better to install on the higher position as like 3rd floor In order to be supplied naturally without a motor supplying the material.
7. Dipping machine is equipped with leaching tanks and drying furnace in the following quantities.
1) Leaching water tank; 7 sets
(1) The leaching water is heated by an immersion type electric heater system.
2) The 7th leaching water tank is always supplied with a constant amount of fresh fresh water (the supply amount is adjusted according to the state of residual DMF in the coating gloves). And the overflowing water from the 7th leaching water tank continues to flow into the next leaching tank in the following order from the 6th to the next.
▣ 7th tank(continuously feeding new fresh water; 4~5 tons/24hr)→→water overflow→→6th tank→→water overflow→→5th tank→→water overflow→→4th tank→→water overflow→→3rd tanks→→water overflow →→2nd tank →→water overflow→→1st tank (collect DMF water (4~5 tons/24hr) & transport to DMF purification system by motor pump.
3) DMF coagulator; 1 set
(1)This coagulator is contained some percent DMF for keeping Pu coating thickness & quality. Actually, DMF content is very important. So, it is better to check the DMF content frequently.
4) Drying furnace; 3 sets
-Drying furnace consists of 3 zones. Because wet PU coated gloves must be dried at different temperatures in each of the 3 sections, it has the effect of promoting the evaporation of residual DMF in the coated gloves and increasing the wear resistance.
8. Leaching water cannot be used for groundwater that has not been purified. Iron and other components in groundwater can corrode or rust all moulds and steel parts.
(1) Industrial water is mainly used, or in the case of groundwater, it must be completely purified and used by the R.O system.
9. Use electricity and frequency; 380V or 410V / 50 HZ (In the case of Kolkata area, infrastructure facilities including electricity are very poor. The supply of electricity is unstable and the voltage difference is too large. If the supply voltage is large, there is a problem in heating, and In addition, there are cases of damage to the machine operation and machine control system It is necessary to prepare to supply stably without voltage deviation.
(1) So, we recommend installing a generator with an appropriate capacity and quantity in case of unstable electricity supply.
(2) Also, most of the electric and electronic parts are damaged by the unstable supply voltage. Therefore, we recommend that customers install an automatic voltage regulator (AVR) with an appropriate capacity.
10. And this dipping machine uses electrical system to heat leaching water (immersion heaters)
(9); Fin type heaters for drying furnace (chamber)
11. 4 sets of panels are installed for precise and stable operation and control of the dipping machine.
(1) 1st; machine main panel
(2) 2nd to 4th; temperature control of the leaching water and drying furnace
12. 6 CCTV cameras are installed to check and control the dipping machine operation.
13. And install an automatic takeout unit for coated gloves that are dried after coating.
14. We will proceed with the following process according to the contract terms after confirming all the machine specifications of the dipping machine with the customer.
(1) At the same time as the contract of the machine, we will provide the necessary machine drawings and assembly drawings.
(2) We will provide all programs and curriculum for customer (one person) education with receipt of down payment.
(3) The training period starts on the basis of 25 days. In addition, during the period of education, accommodation and transportation are provided by PLAMA.
(4) The customer is responsible for the round-trip airfare and stay expenses for trainees dispatched by the customer.
15. If you need, I will introduce the equipment needed for Lap equipment for PU coating gloves production.
16. And if you need, I will discuss with you about DMF water purification system and DMF fume scrubber system for recovering DMF.
17. We will supply the dipping machine for you to choose from the following two conditions.
1) Knock down condition;
(1) We will send all machine parts to the customer without assembling the dipping machine. In addition, the customer's factory will proceed with the assembly, installation, and commissioning process with the customer's assistance.
(2) Required container quantity; 40 ft HQ container; 5 ea
(3) Time of delivery; 80 days from the date of receipt advance payment.
(5) period of assembly, installation and commissioning of the dipping machine; approx. 90 days
(6) We will send 3 technicians and 1 electrician to assemble and install the machine.
a) Technician (3 persons); approx. 80 days
b) Electrician (1 person); approx. 20 days
c) Chemical specialist for operating and training; approx. 10 days
(7) When assembling the machine, we need customer assistance as follows; (approx.)
a) Assembly helper; 3 persons (70 days)
b) Electrician (skilled ball); 2 persons (20 days)
c) Welder (skilled ball); 2 persons (65 days)
d) Painting (skilled craftsman); 2 persons (70 days)
(8) We need the following equipment and tools for machine assembly and installation.
a) Forklift; 15 tons---2 sets
b) Hammer drill; 1 set
c) Welding machine; 2 sets
(9) Assembly of dipping machine starts after all machine parts are removed from container.
(10) Start assembling each part of the dipping machine.
(11) Main gate size of the factory for entering all machine parts;
-W * H; 6m * 4m
NO | ITEM | PUD (water based) dipping machine | DMF PU dipping machine |
1 | Kinds of dipping gloves | PUD gloves / NBR foam gloves *This machine can dip 2 different type gloves. *But this machine cannot PU(DMF) Dip. | PU gloves with DMF solution. *Exclusive PU (DMF) coating gloves |
## | Dipping machine type | Vertical running | Horizontal running |
2 | Cost of each resin | PUD (water based) resin; Approx.USD5.8/kg | PU resin; Approx. USD1.63 / kg |
3 | The amount of residual DMF | DMF free | Contained DMF ingredient |
1) Traditional PU polymerization involves organic solvents like DMF, dimethylformamide, to control PU viscosity so that the PU can be easily processed and coated. (1) DMF is a colorless moisture-absorbing liquid with a pungent odor and high boiling point, soluble in water, alcohol, and acetone. Organic solvents emitted during traditional PU processing would eventually become greenhouse gases, solvent elimination consumes a lot of energy, and the traditional process cannot completely eliminate DMF from the product. Sometimes, residual solvents might induce respiratory disturbances in patients with a weak respiratory system (like asthmatic patients). EU and other nations have listed DMF as a restricted toxic substance. Various renowned European sellers have demanded that the products be DMF-free, which we (Ocean Plastics) can achieve. Note: DMF is also sometimes referred to as DMFA. Various major gloves dealers in Europe and the United States and other developed countries have requested DMF-free PU coated gloves where possible. (2) Currently, bulk purchasing companies in Europe and the United States require residual DMF standards of PU gloves to be less than 100 ppm. There is a tendency to lower the residual DMF standard every year. Therefore, MAJOR PU gloves production company soaks PU gloves in industrial water for 2 days after taking them out from the dipping machine. It is then dehydrated and dried again and supplied to customers. Gloves that have undergone this process become almost DMF free PU gloves. -Liners fitting⇒⇒⇒Gloves PU dipping⇒⇒⇒Excess resin Finger drops and Spills ⇒⇒⇒ Coagulation process of coating gloves in the coagulant tank⇒⇒⇒Processing 1st-2nd-3rd-4th-5th-6th-7th Leaching water tanks for elimination DMF and chemicals from the coating gloves⇒⇒⇒1st-2nd-3rd Drying furnace for drying & exhaust DMF smell from the coating gloves⇒⇒⇒Automatic takeout of the finished coating gloves
2) Water base PUD resin is a kind of synthetic NBR resin. Therefore, in order to produce PUD coated gloves, it is necessary to immerse liners in a water base pretreatment (Coagulation) solution before PUD coating work process. The solution used for pretreatment (Coagulation)and process is as follows. -Pretreatment Coagulation) solution; Water + Calcium Nitride + other -Liners fitting⇒⇒⇒Pretreatment (Coagulation)⇒⇒⇒Excess solution spill from the liners⇒⇒⇒Gloves PUD dipping⇒⇒⇒Coagulation process of coating gloves in leaching water tank⇒⇒⇒Processing 1st rain shower of coating gloves⇒⇒⇒2nd-3rd Leaching water tanks processing for elimination chemicals from the coating gloves⇒⇒⇒1st-2nd-Drying furnace for drying the coating gloves⇒⇒⇒Automatic or manual takeout of the finished coating gloves
| |||
4 | Machine dimension (L*W*H) | 40m * 3.4m * 5m | 61m * 2.8m * 6.7m |
1) Total length of PUD dipping machine is short compare with PU dipping machine. Because, in case of PUD dipping, there is no need for strong chemical leaching process because DMF solution is not used. Only three leaching tanks are installed to elute some of the additives remaining in the coated gloves. Thus, water, electricity and all other utilities can be saved. 2) Total length of PU dipping machine is very long comparing with PUD dipping machine. Because PU resin must be mixed with DMF for coating. Since this DMF solution is a very harmful substance, it is necessary to reduce residual DMF from coated gloves. We continue to increase the number of chemicals leaching tanks to meet the residual DMF standards required by European and American buyers. Unfortunately, however, there are limits to reducing the amount of residual DMF. And recklessly increasing the number of leaching tanks increases the length of the machine and increases the cost of water, electricity and other utilities. This is a very important issue, please see. | |||
5 | DMF recovery system & Scrubber system | Not need | 2 systems must ready |
6 | Wastewater treatment system (ETP) | Wastewater coagulation and settling tank (Very simple type) | Not need |
7 | Knitted liner | 15 gauge, 18 gauge | 13 gauge, 15 gauge, 18 gauge |
8 | Quantity of leaching water tank | 3ea including a rain shower tank | 7ea water tanks |
9 | Quantity of hot water circulation pump motor | 3ea | 6ea |
10 | Quantity of water transfer pump motor | 3ea | 5ea |
11 | Type of Leaching water heater | Electric immersion heater | Electric immersion heater |
12 | Output capacity (hr) | 500~850 pairs | 900~1500 pairs |
13 | Mould quantity | 1120 pairs | 1800 pairs |
14 | Drying furnace | 2 zones | 3 zones |
16 | Type of drying heater | Electric Fin heater | Electric Fin heater |
17 | Industrial water usage, electricity usage and other utilities costs. | It decreases by about 2 times. | The cost increases by about twice. |
17 | Additional dipping tray for pretreatment (Coagulation) | Water + Calcium Nitride * This unit is a process that must go through to produce all kinds of Nbr coated gloves. | Not need |
18 | Merit of PUD and PU gloves | 1) There is no DMF recovery system, so the cost of utilities is low. 2) Labor cost is low. 3) Residual DMF is free | 1) Due to the high physical strength of PUD, the wear resistance of GLOVES is high. Therefore, there is a large demand in the relevant market. 2) The production of PU Coating gloves is more than 76% higher than that of PUD gloves. 3) There is no cost of coagulation or coagulant in PU coating. 4) Recover about 95% of high-purity DMF from the DMF recovery system and reuse it. |
19 | Demerit of PUD and PU gloves | 1) The physical strength of PUD resin is low, so the abrasion resistance of GLOVES is very low. Therefore, demand in the relevant market is limited. 2) Raw material cost is 3.5 times higher than DMF PU. 3) Before applying PUD coating, it must go through a Coagulation process. 4) And the cost of the coagulant is incurred.
| 1) Labor and utilities costs are incurred due to the DMF recovery system. 2) Residual DMF must be kept below 100 ppm for export to European or American markets. For this purpose, the firstly produced PU gloves should be soaked in water for about 48 hours. And it has to go through the process of dehydration and re-drying. However, in other regions, the demand for PU gloves below about 4000ppm is increasing. |
18 | Actual necessity power 1) This is a case of using an Electric Heating System for heating of leaching water and heating of drying chamber. | 295 kw ? | 360 kwh ? |
♣ I’d like to recommend the DMF PU dipping machine.
1) PUD coated gloves are gradually being replaced by NBR foam or Glossy coated gloves.
2) This is because not only the cost ratio is increasing due to raw materials and productivity, but also the market demand for NBR gloves is changing due to the low abrasion resistance due to the strength of physical properties.
3) And the most important final conclusion is that the water based PUD dipping machine can produce both NBR Foam gloves and Glossy gloves. So, if you need to, you can also review how to produce PUD gloves as well when purchasing NBR gloves dipping machine.
PLAMA |
I'm here for you
## MAIN SPECIFICATION OF HORIZONTAL RUNNING MACHINE
FOR GLOVES PU DIPPING.
SPECIFICATION |
| |
MODEL | PMOHY-HD60MG-1800M-PUM | |
COMPOSITION OF COMPLETE LINE | 6 PLATFORMS/TOTAL LENGTH 62 meters | |
PRODUCTION CAPACITY(ON THE BASE OF PALM FIT COATING) | 900-1550 PAIRS/HR | |
MOULD LINK BRACKET | 3600 pcs(TOTAL) | |
TOTAL NUMBER OF GLOVE MOULD | 1800 PAIRS(3600 CAVITIES) NEW MODIFIED MOULD (HAND AND WRIST.) | |
PITCH OF MOULD LINK | 200 mm | |
TOTAL LENGTH OF CHAIN/1 ROW | 359 meters | |
-CHAIN CAN EASILY REPLACE AT THE NEAR POSITION FROM GLOVE FITTING ROOM. -TENSILE FORCE OF CHAIN CAN EASILY REGULATE BY TENSILE SPRING SYSTEM. | ||
MAIN DRIVING MOTOR | AC 3.75 kw WITH REDUCTION GEAR(RATIO—200;1) ## 6 PHASE 380V/50 hz/60 hz | |
DRIVING SYSTEM | CHAIN DRIVE WITH GEAR | |
MAIN CONTROL SYSTEM | PLC CONTROL & ELECTRIC PARTS MADE BY LG KOREA ; ALL OF MACHINE CONTROL IS AVAILABLE BY DESK TOP COMPUTER AND TOUCH SCREEN MONITOR | |
OPTIONAL; THE BUYER MUST MAKE WIRING AND CONNECTION ELECTRIC CABLE FROM MAIN PANEL TO PU DIPPING LINE. | ||
PU RESIN MIXING TANK(GEARED MOTOR) | 1.5 kw ☓2 sets= 3.0 kw (900 ltr * 2 sets) SIZE; Ø1000 *1100 kgs | |
PU RESIN SUB-TANK(GEARED MOTOR) | 0.75 kw ☓2 sets= 1.5 kw (400 ltr * 2 sets) SIZE; Ø800 *1000 kgs | |
PU RESIN FEEDING PUMP(GEARED MOTOR) | 0.75 kw ☓2 sets= 1.5 kw 2 sets | |
GLOVES PU DIPPING TRAYS
| 2 sets (1.08 * 0.31 * 0.1m) FOR PU GLOVES COATING -COMBINED USING FOR PALM & HALF PU COATING. | |
PU RESIN AGITATOR OF THE DIPPING TRAYS | 2 sets ☓200 w =400 w (INDUCTION MOTORS) | |
PU RECOVERY PUMPS FOR RECYCLING | AIR OPERATED DIAPHRAGM PUMPS; 2 sets | |
FLYING RAIL SYSTEM * EACH FLYING RAIL UNIT INCLUDED A PNEUMATIC CYLINDER FOR UP & DOWN MOVEMENT. | -PU DIPPING LINE HAS 4 FLYING RAILS AT NEAR THE DIPPING TANK. * THESE FLYING RAILS ARE UP & DOWN DEPEND ON GLOVE DIPPING POSITION & DIPPING OR NOT. * PNEUMATIC CYLINDER; 4 sets | |
IMPELLER SYSTEM FOR STIRING PU RESIN | FOR PU FOAM COATING; 600 rpm | |
DEHUMIDIFIER FOR PU DIPPING LINE | 198 cm2(40 ltr/day) * 4 sets -DIPPING CHAMBER; 2 sets -AMONG 1 st SECTION AND 3 SECTION; EACH 1 set | |
COAGULATORS TANKS FOR COATED GLOVES(2 sets) | TANK(RIGHT & LEFT) DIMENSION; L * W * H; 3.05 m* 0 574m * 0.4m----2 sets | |
♣ 8 LEACHING WATER TANKS INSTALLED GAS FIRED BOILERS FOR LEACHING WATER HEATING. ♣ THREE DIVIDED DRYING CHAMBERS ARE ALSO HEATING BY GAS BURNERS AND THEN HEATED HOT AIR FEED INTO 3 ZONE DRYING CHAMBERS BY EACH FAN. AND HOT AIR SPREAD UNDER THE GLOVES BY MANY SMALL HOLES WITH THE PLAIN SHAPE. ♣ ABOVE LEACHING WATER TANKS AND DRYING CHAMBERS ARE HEATING BY GAS FIRED BOILERS AND BURNERS . | ||
LEACHING WATER TANKS FOR EXTRACTION DMF(LOCATED ON THE GROUND FLOOR)
| 1 st TANK(L * W * H); 16.17 m* 554mm * 400mm * THIS LEACHING WATER TANK HAS 4 HOLES FOR DMF WATER DRAIN AND OTHER PURPOSE. * HOLE SIZE; 40 Ø * THIS TANKS ARE INSTALLATION 2 DRAIN PUMPS | |
2 nd TANK(L * W * H); 17.52 m * 554mm * 400mm | ||
LEACHING WATER TANKS DIMENSION FOR EXTRACTION DMF(LOCATED ON THE 2nd LEVEL OF 2 nd FLOOR) | 3 rd TANK(L * W * H); 20.15 m * 554mm * 400mm 4 th TANK(L * W * H); 17.85 m * 554mm * 400mm 5 th TANK(L * W * H); 19.25 m * 554mm * 400mm | |
LEACHING WATER TANKS DIMENSION FOR EXTRACTION DMF(LOCATED ON THE 3rd LEVEL of 2 nd FLOOR) | 6 th TANK(L * W * H); 14.94 m * 554mm * 400mm 7 th TANK(L * W * H); 15.17 m * 554mm * 400mm 8 th TANK(L * W * H); 14.98 m * 554mm * 400mm | |
WATER VOLUME OF EACH WATER TANK | 1 st TANK ; 3.73 tons/ 2 nd TANK; 3.93 tons 3 rd TANK; 4.43 tons/ 4 st TANK; 4.03 tons 5 th TANK; 4.15 tons/ 6 th TANK; 3.44 tons 7 th TANK; 3.43 tons/ 8 th TANK; 3.43 tons TOTAL 30.67 tons | |
HOT WATER CIRCULATION MOTOR PUMPS ; 6 sets | *6 sets X 0.2 kws=1.2 kw | |
WATER TRANSFER PUMP MOTORS; 5sets | *5 sets X 0.4 kws=2 kw | |
GAS FIRED BOILER SYSTEM; 1) WATER HEATING FOR CHEMICAL LEACHING; -6 GAS BOLIER NEAT AT EACH WATER TANKS ON THE GROUND.
* POWER CONSUMPTION
2) FOR DRYING CHAMBERS & HOT AIR FEEDING UNIT; (1) HEATED AIR FEEDING & CIRCULATION SYSTEM INCLUDING HEATERS. -HOT AIR SPREADING SYSTEM WITH SMALL HOLES ON THE STEEL SHEETS.----- ea -AIR FEEDING DUCTS.----3 sets
* HOT AIR FEEDING TEMPERATURE (2) GAS BURNER * POWER CONSUMPTION OF HEATERS
(2) DMF FUME EXTRACTION FAN MOTOR & DUCTS CONNECTED WITH 2 nd FLOOR. | TOTAL 6 GAS BOILERS * AUTOMATIC SENSORS INCLUDED; -WATER MAX. LEVEL SENSORS; 6 sets -TEMPERATURE SENSORS; 6 sets
6 sets X 2.08 kws =12.48 kws * GAS BOILERS CAN ADJUST OWING TO PU COATING SITUATION & TEMPERATURE SITUATION. * AUTOMATIC TEMPERATURE CONTROL SYSTEM. HOLE SIZE; 18 Ø
-TEMPERATURE SENSING SENSOR INTO CHAMBERS; 3 sets -OVER HEATING TEMPERATURE SENSING SENSORS; 3 sets(MAX. SETTING 300 ℃)
150 ℃ TOTAL 3 GAS BURNERS 3 sets X 3 kws =9 kws
3sets: 5.5kw 4p | |
COATED GLOVES TAKE OUT DEVICE FROM THE GLOVE MOULDS. | PNEUMATIC CYLINDER WITH GRABBER | |
SUPERVISORY CCTV & MONITORS | 5 CCTV & 4 CHANNELS MONITOR -GLOVE TAKE OUT POSITION; 2 sets -PU DIPPING POSITION; 2 sets -COAGULATORS; 1 sets | |
TOTAL ELECTRIC CONNECTED POWER | 40.33 kws | |
★★★★★★★★★★★★★★★★★★★★★★★★★★★★★★★★★★★★★★★★★★★★★★★★★★★★★★ | ||
RECOMMENDABLE PART THE BUYER; | ||
AIR CONDITION SYSTEM | THE BUYER SCOPE | |
DEHUMIDIFIER |
| |
CAPACITY OF DUHUMIDIFIER | 99 m3 | |
DEHUMIDIFYING VOLUME | 33 ltr/DAY(TEMP. 27C/HUMIDITY 60%) | |
ADVISIBLE QUANTITY OF DEHUMIDIFIER | 4-5 sets | |
|
| |
SPARE PARTS BY THE SELLER; |
| |
MOULD BY EACH SIZE | 5 pairs * 7 kinds 35 pairs | |
FULL ARM LINK BODY | 100 pcs | |
CHAIN | 10 meters | |
PNEUMATIC CYLINDER | 2 sets | |
CARTRIDGE HEATER FOR WATER TANK | 2 pcs | |
HEATER FOR DRYING CHAMBER | 1 pc | |
ELECTRIC PART * MAGNET * RELAY | FULL SETS * 3.75 kw; 2 sets * 10 EA | |
TOTAL ELECTIRC POWER |
| |
MACHINE DIMENSION(L * W * H) | 61668 * 2821 * 6792 mm | |
|
| |
|
|
|
- Product Info Attached File
B2B Trade
Price (FOB) | Negotiable | transportation | Ocean Shipping |
---|---|---|---|
MOQ | Negotiable | Leadtime | Negotiable |
Payment Options | L/C | Shipping time | Negotiable |
PLAMA WORLDWIDE TECH CO., LTD
-
16
- President
- David-h RHYU
- Address
- (room 1224, Seogwipo-si, Jeju-do, Korea
- Product Category
- Other Construction Material Making Machinery,Other Packaging
- Year Established
- 1998
- No. of Total Employees
- 1-50
- Company introduction
-
Plama Worldwidetech Co., Ltd was established in 1998. In the early days of the business, wemanufactured and exported specially designed extruders, blow molding machines,and CCL (coil color coating) machines, and gained the respect and trust of manyoverseas customers. In addition, our company manufactures and exports speciallydesigned dipping machines to Southeast Asia, Central and South America, andAfrica. The demand for specially coated gloves is expanding as they arerequired in all industrial and construction sites and in the assembly processof precision machinery, including automobiles. The horizontal running type dipping machine is optimized for theproduction of PU, Nitrile (Glossy/Foam/Water Spray) coating gloves. TheVertical running dipping machine is optimized for the production of NitrileSandy fishing and Crinkle gloves. The countries we manufacture and supply toour customers abroad are Vietnam, Spain, Turkey, Chile, Uzbekistan, Ukraine,India, Russia, Iran, Argentina, Bangladesh, Sri Lanka.
Our goal is tobe a family for life, providing our customers not only with the best qualitymachines, but also with trust, faith, and credit. Our R&D center is stillworking today to develop new quality machines and equipment until all customersare satisfied. And the supply of all kinds of machines is accompanied byprofessional consulting service, including feasibility, engineering, totaldesign, training, and technical assistance.
- Main Markets
-
India
Indonesia
Kazakhstan
Russia
Turkey
- Main Product
- Attached File
Related Products
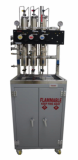
Solvent Purification System, Solvent Distillation
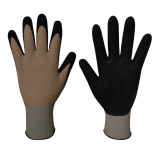
Natural Grip200 Corn-NBR Sandy coating gloves
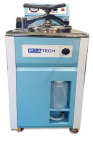
Autoclave-Pressure Cooking Tester/PCT
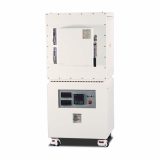
SIC Muffle Furnace
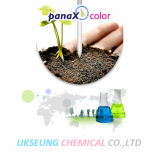
Panax Eco-Friendly Pigment