Blast Furnace -Dewatering Device
Negotiable Min Order Quantity Unit
- Required Quantity
-
- Place of Origin
- Payment Terms
- Negotiable
- Production method
- Negotiable
- Shipping / Lead Time
- Negotiable / Negotiable
- Keyword
- Category
- Other Machinery & Industry Equipment
Sekyung Corporation
- Verified Certificate
-
17
Product name | Blast Furnace -Dewatering Device | Certification | - |
---|---|---|---|
Category | Other Machinery & Industry Equipment | Ingredients | - |
Keyword | - | Unit Size | - |
Brand name | - | Unit Weigh | - |
origin | Stock | - | |
Supply type | - | HS code | - |
Product Information
Handling of blast furnace slag is an important aspect of modern blast furnace operation. Today, blast furnace slag is a saleable product (granulated slagsand for production of cement) rather than a difficult and costly waste material. Paul Wurth has developed the INBA® slag granulation process (incorporating our proprietary dynamic INBA® dewatering drum) as the most popular and effective means of processing blast furnace slag in the world today.
The process is highly flexible; and the compact sub-plant can be applied to any furnace configuration. Granulation, dewatering and storage of the slag can be done adjacent to the furnace or can be split up to suit available plant space or logistics. With the dynamic nature of the process (slag is granulated and dewatered at the tapping rate from the furnace) the operator can receive slag flowrate data from the INBA® plant. This data is useful in controlling and optimising the blast furnace process. Important Benefits:
Very compact design offering maximum flexibility in the layout of installations adjacent to the cast floor of the blast furnace. With an adequate layout of the hot runners on the cast floor, or through the introduction of an additional remotely located second granulation tank, one granulation unit can handle the slag of two tap holes.
Continuous filtering and evacuation of dewatered slag sand up to its storage facility without interruptions for purging.
Low fines content in the closed loop water circuit
High reliability
Measurement of slag flow, due to the design of the drum and the dewatering process.
Flexibility of the plant operation to be largely independent from blast furnace operations, such as tapping time duration, inter-cast gap time, minimum and maximum slag flows, etc.
Air pollution control through closed loop water circuits and reduced emissions
Low investment costs compared to static and other dynamic dewatering systems.
Low wear on drum body and therefore life time in excess of one BF campaign - due to virtually no relative movement between slag and the dewatering equipment.
Low maintenance cost due to low wear.
Low operation costs due to low energy consumption, simple design and fully automatic operation.
B2B Trade
Price (FOB) | Negotiable | transportation | - |
---|---|---|---|
MOQ | Negotiable | Leadtime | Negotiable |
Payment Options | Negotiable | Shipping time | Negotiable |
- President
- Jaenam Shim
- Address
- 1305 East Wing, Hanshin Intervalley Bldg. 322 Tehran-ro Gangnam gu, seoul, Korea
- Product Category
- Auto Batteries & Starter
- No. of Total Employees
- 1-50
- Company introduction
-
Sekyung Corporation was established in 1989 for manufacturing and supply of Magnesia Products in North Korea and Ferro Alloy in South Korea.
We have built our plants in Dancheon of North Korea to produce quality product of Dead Burned Magnesite for refractory use, and Caustic Calcined Magnesite for desulfurization agent and fertilizer.As you may know Magnesite ore from Dancheon North Korea is very famous for the high MgO content ranging from 46.5-46.7% and production facilities has furnished from South Korea to manufacture and supply of consistent quality products and diversify the source of Magnesite to maintain the international market in stable status.
We also produce Monolithics Basic Refractories with high quality North Korean D. B. MgO to distinguish our products in quality with any other sources and this is proved by POSCO and INI Steel Co., Ltd in South Korea.
Daeheung Talc Mine in North Korea has formed in the same time together with Haicheng Mine in China and being kept as untouched status. So, investment to the Talc Mine was attracted and our investment to produce the high whiteness filler grade Talc for PP compound have accomplished to meet the requirements in S Korea and Oversea Market. And this Talc used as a Filler of PP Compound has proved No Smell during plastic molding process at high temperate by the Samsung and LG Chemical Co., Ltd.
We are cooperating with a shipping company in Korea for chartering vessel according to the volume of order and currently one vessel with 2,000MT capacity is regularly serving from Heungnam or Kimchack Port in North Korea to any ports in North East Asian countries under our instruction, Serving to North America and Europe with large vessel is also possible since 4,000M2 warehouse in the Kimchack loading Port is already provided for large quantity cargo.
- Main Product
Related Products
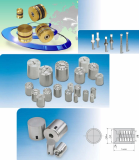
Date Pin (Date Core)
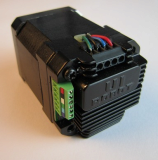
NEMA17 42mm stepper motor with driver or controller
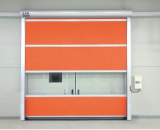
High Speed Door_ KAD-2000, cua cuon nhanh
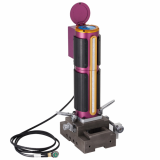
AIS3000 HD
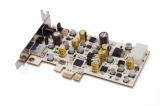
Audio Grade PCIe Host Card – tX-USBexp